Injection Moulding Part Costs
Among various manufacturing processes in the plastics industry, injection molding stands out as a highly favored method. Its efficiency, repeatability, and precision in creating parts to fit within strict tolerances make it a go-to option for the mass production of plastic components. Everyday objects that we come into contact with, like the TV remote in your hand or the protective housing of your fan, are just a few examples of items that are brought to life through the power of injection molding.
The injection molding industry, despite its pivotal role in our daily lives, is not without its challenges. One of the primary difficulties lies in the lack of injection moulding costs standardization. This void leads to a broad spectrum of quotes given by injection molding vendors to manufacturers, leaving the latter in a quandary about the appropriate amount they should be budgeting for their desired products.
In response to this issue, we at Trumould are spearheading an initiative aimed at eliminating this uncertainty from the quotation process. Our belief is rooted in the premise that a designer should not have to wait anywhere between 5 to 10 days to receive a quote from a vendor. Instead, we argue that there should be a well-defined, systematic approach in place to calculate costs, thus enabling designers to predict what the expenses should be and adjust their designs accordingly.
As a testament to our commitment to this cause, we have created Trumould’s Auto Quoting Engine. This unique solution is geared towards not only making procurement more efficient but also revolutionizing the entire injection moulding costs estimation process.
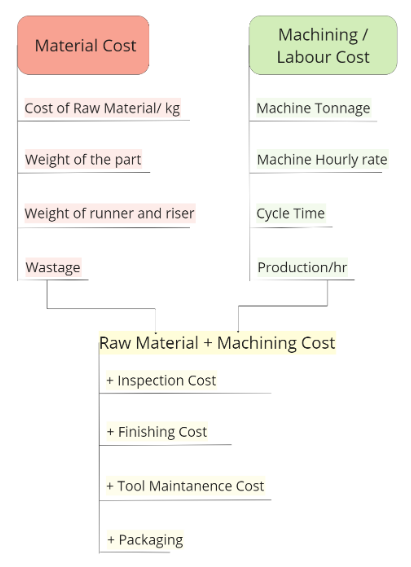
The Emergence of On-Demand Injection Molding
On-demand injection molding is rising in popularity due to the shift in consumer and market demand. Modern customers prefer personalized products, and the market is increasingly becoming volatile. On-demand manufacturing facilitates flexibility and quick adjustments to these ever-changing demands.
Furthermore, digitalization has paved the way for this shift. With digital platforms, companies can now easily upload their design files, get instant quotes, and place orders. This technology has significantly reduced the lead time compared to traditional manufacturing methods. Trumould is pioneering this shift in injection molding by developing a tech-enabled platform that specifically solves injection moulding costs issues.
Material Cost
- Cost of Raw Material: The universe of injection molding boasts of a diverse range of over a thousand potential plastic materials. This factor significantly drives the final cost of the molded parts. Given that some materials are considerably more expensive than others, we encourage our clients at Trumould to draw on our vast reservoir of knowledge regarding plastics. This way, we can help them select a material that meets their requirements but also stays within budget constraints. It's also worth noting that the cost of raw material has shown considerable fluctuations over the past 3 to 4 years, making it the most volatile element of this cost calculation.
- Part Weight: The weight, or more accurately, the volume of the part, is another key contributor to the overall cost. While the vendor's influence over this aspect is limited, our general advice to designers at Trumould is to aim for thinner walls to reduce weight, unless the design necessitates additional weight for structural integrity.
- Weight of Runners and Risers: While the weight of runners and risers might seem trivial, it becomes significant in large-scale production runs. To mitigate these costs, we propose the use of hot runners, while also considering the production volume necessary to offset their additional expense. We've developed a method at Trumould to systematically calculate runner weight based on part geometry and gate location.
- Wastage: Certain unavoidable wastage occurs during the injection molding process, primarily during changeovers. If a prior production run used a different material, the vendor must clear out all remnants of the previous plastic before embarking on a new batch. This requirement leads to a considerable amount of waste. Other sources of wastage can include machine errors, human mistakes, or substandard batches of plastic.
Labour Cost
- Machine Tonnage: The tonnage of a machine is an integral aspect of cost calculation. It impacts the required injection pressure based on the size and complexity of the part. Machines with higher tonnage, necessary to keep molds securely closed during the injection molding process, come with higher operational expenses. These expenses cover real estate, utilities, and maintenance costs
- Machine Hourly Rate: The injection molding operation is a multifaceted process requiring the skills of several professionals. Programmers control the mold's parameters, such as temperature, duration, opening, and closing timings. Production managers oversee the optimal utilization of machines, while operators handle part replacements and ensure smooth mold functioning. In addition to these labor costs, the constant running costs of the machine also contribute to its operating expenses. Trumould, in response, has developed a systematic standardization of hourly rates based on the tonnage of the machine. This extensive data forms a pivotal component of our innovative Auto Quoting Engine, providing designers with the tools they need to estimate the pricing of their parts accurately and effortlessly.
- Cycle Time: Cycle time is a significant player in the cost determination game. It's the total time spent on the entire process from the mold's closure, cavity filling, material cooling, to the part's ejection. The lion's share of this time is usually consumed by cooling, which can take anywhere from a few seconds to a full minute. Optimization of the cycle time can be achieved by improving the cooling process of the mold or selecting a material that cools more rapidly. At Trumould, our extensive experience and in-depth knowledge enable us to estimate cooling times with remarkable precision based on the part's geometry and material properties.
- Production Rate: The production rate, defined as the number of parts that can be produced in an hour, is the final piece of the puzzle in calculating the machining cost. It is dependent on a number of variables such as the number of cavities in the mold, the cycle time, the efficiency of the process, and the total quantity of parts that need to be molded. Once the production rate is known, the calculation of the machining cost becomes a simple mathematical operation. Trumould's well-organized process allows us to predict our efficiencies with an accuracy of over 90%. This impressive degree of precision plays a significant role in the success of our auto quoting engine.
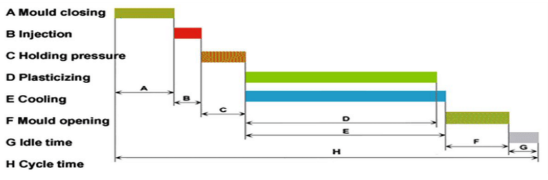
Material Cost
- Inspection Cost: Once the part has been manufactured, it is essential to conduct a thorough Quality Control check. This step ensures that the part has been produced according to the specified standards. Our specialized personnel meticulously inspect the parts, looking out for any potential defects that may have occurred during the molding process. We employ statistical process control to determine the optimal number of parts to inspect to give us a high degree of certainty that the whole batch is of similar quality. Typically, inspection costs account for about 2-5% of the total part cost.
- Finishing Cost: Depending on the customer's requirements and product specifications, some parts may require post-processing. This could include cleaning off runners and risers that are attached to the part, tapping the part, or part printing. We advise our customers to keep this process to a minimum due to its labor-intensive nature and the difficulty of automating it. The associated costs are evaluated on a case-by-case basis.
- Tool Maintenance Cost: Poor tool management can lead to high repair or replacement costs over time, significantly inflating the total cost of ownership. Regular maintenance can help prevent mold damage caused by vent deposits, which can lead to part defects and unexpected production errors. At Trumould, we divide the cost of tool maintenance across the number of parts produced. This usually amounts to about 1-3% of the part cost.
-
Packaging Cost: The last component of the cost structure is the packaging cost, which typically makes up about 5% of the part cost. Packaging involves three stages and is generally standardized at Trumould, with the exception of industries.
Part-Level Packaging: Each part is individually wrapped to prevent damage during transit.
Box-Level Packaging: This involves optimizing the safe packing of parts in a box.
Shipment-Level Packaging: The final stage includes palletizing and securing the boxes on the pallet.
Trumould Auto Quoting Engine
Trumould with its years of expertise in plastic injection molding domain is able to formalize all these factors and cohesively develop an Auto Quoting Engine. We can quote a injection moulding part costs with seconds using this engine. This not only saves time and hassle but it also helps in benchmarking the cost of the part. Try our auto quoting engine and get part cost instantly, you can also turn the knobs by switching around the materials, quantity and finishes.