What is On Demand Injection Moulding ?
On-demand injection molding is a form of manufacturing, a process that allows manufacturers to produce specific quantities of items as and when they are needed. This reduces the burden of maintaining a high level of inventory, and the risks associated with overproduction or underproduction.
Injection molding is a process where materials are injected into a mold to produce parts or products. The process involves melting plastic pellets and injecting them into a mold cavity where it cools and hardens to the configuration of the cavity. It’s a versatile manufacturing process used for producing parts in large volumes, from the simplest to the most complex shapes.
The ‘on-demand’ aspect means that the injection molding is done based on the actual demand of the parts, leveraging digital platforms to streamline the design, order, and manufacturing process. It facilitates small quantity orders for prototypes or customization in larger batches, thus providing a lot of flexibility and cost-effectiveness for manufacturers.
The Emergence of On-Demand Injection Molding
On-demand injection molding is rising in popularity due to the shift in consumer and market demand. Modern customers prefer personalized products, and the market is increasingly becoming volatile. On-demand manufacturing facilitates flexibility and quick adjustments to these ever-changing demands.
Furthermore, digitalization has paved the way for this shift. With digital platforms, companies can now easily upload their design files, get instant quotes, and place orders. This technology has significantly reduced the lead time compared to traditional manufacturing methods. Trumould is pioneering this shift in injection molding by developing a tech-enabled platform that specifically solves injection molding issues.
Drawbacks of Traditional Injection Molding
Traditional injection molding is an established process that’s been utilized for many years. However, in the face of modern market requirements, certain challenges associated with the procurement process for traditional injection molding have become evident.
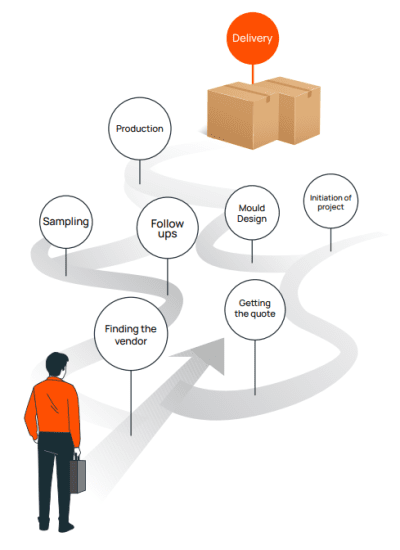
- Finding the Right Vendor: Finding a reliable and qualified vendor is a significant task in itself. Companies must thoroughly research and compare numerous factors, such as a vendor’s capabilities, expertise, production capacity, and past performance. Factors like geographical location, reputation, and ethical practices also matter. All these aspects take time to analyze and the process may result in delays and increased overhead costs.
- Getting a Quote: After finding a potential vendor, the next step is obtaining a quote for the required services. However, obtaining a quote in traditional manufacturing is not a quick process. It usually takes about 5 to 10 business days to receive a quote from the vendor. Furthermore, there can be a wide discrepancy in quotes for the exact same part from different vendors, which can lead to confusion and require further negotiations and discussions.
- Vendor Communication Post-Order Placement: Once the order is placed, communication with the vendor can be another hurdle. Vendors may not always be readily available to provide updates or answer queries regarding the order. This lack of transparency and poor communication can lead to uncertainties and anxiety about when the order will be completed and delivered
- Vendor Causing Time Delays: Vendors failing to stick to their commitments is another significant issue in traditional injection molding procurement. These delays can lead to setbacks in the client’s production schedule, resulting in financial losses and a potential hit to their brand value.
- Lack of Quality Control: Quality control in traditional manufacturing can be hit or miss. Each vendor has their own quality control process, and they may not cover all the parameters important to the customers. This inconsistency can lead to a higher rate of defects, returns, and dissatisfaction.
- Logistical Hassle: Logistics can also be a significant challenge, particularly when dealing with overseas vendors. Customers often have to arrange for their own logistics to get the parts from the vendor to their facility. This not only adds to the overall cost of the product but can also result in delivery delays and increased complexities.
In summary, while traditional injection molding has been a mainstay in manufacturing, the procurement process often leaves much to be desired. The emergence and adoption of on-demand manufacturing, in this context, can be viewed as a response to these challenges, offering more flexibility, speed, and efficiency to better meet the demands of modern production needs.
Advantages of On-Demand Injection Molding
On-demand injection molding is rapidly becoming a preferred choice due to the several advantages it offers over traditional manufacturing. Let’s delve deeper into some of these advantages, supplemented by specific examples related to injection molding.
-
Scalability and Flexibility: On-demand injection molding allows companies to produce small batches for prototype testing or larger quantities for full production runs. It eliminates the high costs associated with producing and storing unnecessary parts, thereby reducing inventory costs.
Example: In the automotive industry, parts like door handles, panels, buttons, and knobs are often needed in limited quantities for prototype vehicles. On-demand injection molding can provide these parts quickly and efficiently, without the need to produce thousands of units upfront.
-
Quick Iterations and Time Efficiency:
The digital nature of on-demand manufacturing facilitates faster design alterations and iterations, reducing the time taken to bring a product to market.Example: Consider the manufacturing of medical devices, which often requires multiple iterations and validation steps before reaching the final design. The on-demand approach allows for swift modifications and adjustments, shortening the product development cycle.
-
Cost Efficiency:
On-demand injection molding has fewer upfront costs, as there’s no need for large amounts of material inventory or storage. Additionally, it provides real-time pricing, helping companies to better manage their budgets.Example: A startup developing a new consumer electronics device can leverage on-demand injection molding to produce parts like casing, buttons, or other components. They can start with a small batch for testing, then ramp up production as demand grows, all while keeping costs under control.
-
Quality and Consistency:
Advanced digital technologies ensure high-quality and consistent results in on-demand injection molding. The process is highly repeatable and offers greater control over production.Example: In the aerospace industry, where precision is paramount, on-demand injection molding ensures every component — from interior cabin fixtures to parts within the engine — meets the exact specifications, maintaining high quality and consistency.
-
Sustainability:
By producing only what’s needed, on-demand injection molding reduces waste. This approach aligns with the growing emphasis on sustainable practices in manufacturing.Example: A toy manufacturer, using on-demand injection molding, can minimize plastic waste by producing to fulfill current demand rather than overproducing and risking excess inventory.
In a nutshell, on-demand injection molding presents an efficient, flexible, and cost-effective approach to manufacturing that aligns with the demands of modern consumers and dynamic market conditions. With its myriad advantages, it’s set to revolutionize the manufacturing landscape.