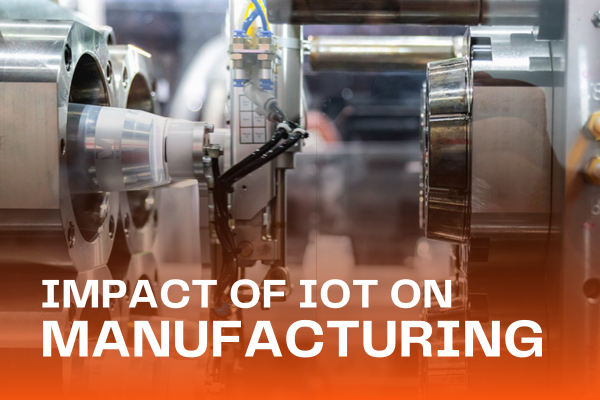
Impact of IoT on Manufacturing
The manufacturing industry is adopting new technology to digitally transform its outdated systems and processes as a part of Industry 4.0. Internet of Things (IoT) is providing enterprises a way to integrate the latest technologies, streamline data flow, and make decisions based on real-time insights.
IoT is integral to smart manufacturing, along with artificial intelligence, machine learning, robotics, big data, and industrial analytics. It is an interconnected set of devices and sensors that collect vital data from the machines to provide analytics for effective decision-making. Statistics show that IoT is likely to have an economic impact of $3.9 to $11.1 trillion on manufacturing by 2025.
Let’s read more about IoT and how it impacts the manufacturing industry around the world.
What is Internet of Things (IoT)?
The Internet of Things is a network of interconnected devices, appliances, vehicles, etc., with sensors that collect and share data in real-time. The devices are also called smart objects (like smartphones, RFID tags, factory machinery, etc.). The devices in the IoT network interact with each other through the internet connection. They exchange data and make autonomous decisions based on the data and pre-defined parameters. Using IoT devices can save time and resources for an enterprise.
The devices will manage warehouse movement, lighting, temperature control, etc., and send alerts for machine maintenance and potential risks. For example, the data from IoT devices can predict a possible gas leak and help solve the problem or vacate the premises to prevent loss of lives.
As per Statista, the projected global Internet of Things spending is estimated at $1.1 trillion in 2023. A report by PwC shows that companies expect to improve all efficiency by 12% by investing in smart technologies like IoT. More manufacturers are expected to embrace Industry 4.0 to survive market competition. Research and Markets report shows the manufacturing industry will spend $276 billion on Industry 4.0 by 2029.
IoT Applications in the Manufacturing Industry
IoT revolutionizes manufacturing by creating more opportunities for innovation and efficiency. It reduces the rigidity of traditional systems to allow manufacturers to act quickly. A few applications of Internet of Things in the manufacturing industry are as follows
• Floor Operations – The factory machinery is fitted with sensors to send real-time data about the machines’ performance. This data is stored and analyzed in the cloud to help the supervisor have a clear idea about the floor operations. It helps continuously monitor production and ensure the machinery doesn’t break down at unexpected times. Additionally, IoT wearables on factory workers can track their health to ensure that hazardous working conditions are not harming them.
• Remote Operations – Modern manufacturers don’t rely on a single factory. They have production units, warehouses, etc., in different locations to increase cost-efficiency. Moreover, outsourcing manufacturing is also common in today’s world. How can the manager control production in a remote factory? The Internet of Things, artificial intelligence, cloud computing, and robotics make it happen. With continuous and real-time data made available, managers can give orders and automate processes in a faraway factory.
• Supply Chain – IoT devices enable the monitoring of trucks and vehicles carrying raw materials and final goods. They allow manufacturers to stay up to date about the inventory in the warehouses, stock in movement, and stock that reached the distributors, etc. Every aspect of the supply chain can be tracked and controlled based on the data provided by the IoT devices.
• Predictive Maintenance – Predictive maintenance of machinery is the most common application of IoT in manufacturing. Enterprises can lose millions due to unexpected equipment failures and breakdowns during production hours. These losses can be avoided by scheduling maintenance sessions during off days. The data sent by IoT devices will alert the supervisor about potential issues in the machines (odd sounds, cracked parts, less efficiency, slower movement, etc.). The supervisor will get the machinery inspected and repaired during the non-production hours before the damage gets out of control.
• Asset Management – Asset management can be considered an extension of predictive maintenance. Factory equipment is a great asset to the manufacturer. By taking proper care of the machinery, manufacturers can increase the life span of each unit and improve their productivity levels. Similarly, the fleets used for transportation, the warehouses with stock, etc., are also managed. Over time, this will result in greater ROI and profits.
• Digital Twins – Digital twins use IoT, AI, ML, and cloud computing. It is where virtual copies of physical objects are created for effective management. For example, the supervisor can experiment with different spare parts or production methods on the virtual equipment to find the best combination and implement it in real life. That way, the actual machinery will not be disturbed or damaged.
What is Industry 4.0?
Also known as the Fourth Industrial Revolution, it is an ongoing transformation from traditional manufacturing to agile and flexible manufacturing by using smart technologies and digital devices. It includes AI, ML, IoT, cloud computing, edge computing, robotics, advanced analytics, automation, 5G, etc., to enhance end-to-end manufacturing processes.
Many enterprises are actively joining the revolution to strengthen their position in the global markets. This has also led to more structured and balanced B2B partnerships between manufacturers. For example, Trumould Injection Molding Company uses advanced systems like Autoqouting and MUD technologies to provide premium-quality manufacturing solutions for cost-effective prices. We partner with MSMEs and large enterprises to provide customized components and goods manufactured using the latest injection molding techniques.
Impact of IoT on Manufacturing
• Greater Efficiency – Internet of Things (IoT) devices help automate recurring tasks and optimize processes to shorten the production cycle without compromising quality. The sensors monitor equipment performance to detect and help resolve issues before they flare into major breakdowns. Production will be continuous and smoother with fewer disruptions. This increases the efficiency of the factory unit.
• Cost-Effectiveness – IoT promotes cost-efficiency in many ways. For example, predictive maintenance reduces the need to spend more money on new machinery. Asset management optimizes the equipment, fleet, etc. Warehouse management, such as temperature control and inventory arrangement can minimize the number of damaged goods. The manufacturer can save money on multiple levels.
• Data-Driven Decision-Making – The core purpose of investing in IoT devices is to generate operational data. This data is stored on the cloud and used to derive accurate, actionable insights. The top and mid-level managers use this information and analytical reports to stay updated about the enterprises’ overall performance and make the most of market opportunities. It also helps avoid risks and pitfalls.
• Better Customer Experience- Customer satisfaction is a must in a competitive world. Manufacturers have to shift from a product-centric to a customer-centric approach to ensure their target audiences are happy with the products and services. IoT automates recurring processes and eliminates the risk of error, thus minimizing the risk of defective products. It also shortens the supply chain by eliminating unnecessary participants.
• Higher Production Rate – When the IoT devices are fitted to the factory machinery, they send real-time data about production and machine health. This gives manufacturers more control over the production cycle. It helps increase the production rate while ensuring the equipment doesn’t get damaged or overworked. Enterprises can manufacture more stock in less time.
• Faster Time-to-Market – We live in a fast-paced world where customers want quick results. That means manufacturers have to speed up the time-to-market period by eliminating waiting times. The real-time data from IoT devices enables faster decision-making. It also helps effectively handle market fluctuations and avoid losses. When combined with Autoquoting technology by Trumould, manufacturers can cut down the time required to take a product from concept to commercialization.
• More Safety for Workers – IoT devices have a crucial role in improving workplace safety. The sensors fitted to the equipment and the wearables on the workers collect data about the danger levels in the factory. From detecting potential accidents to alerting about the change in the atmosphere or the increase in harmful emissions, IoT works in many ways to improve the safety of workers onsite.
• Improved Visibility – Manufacturers can make the right decisions when they have a clear picture of where things stand. When does the equipment need replacing? What are the risks faced by workers? How long will the inventory last? How much time does it take to get raw materials from the suppliers? The answers to these questions can be derived by analyzing the data collected through IoT devices. They provide greater transparency and control.
• Smart Assembly – Smart assembly is where the IoT networks close the distance between manufacturers and customers. This is done in many ways, such as remotely controlling the applications, minimizing downtime due to machine breakdowns, etc. A smart assembly is capable of running itself with minimum intervention from humans. It is efficient, resilient, automated, and productive.
• Better Inventory Management – IoT devices track inventory movement from the factory unit to the warehouse to the end user. They monitor the entire supply chain and help with quality control. From managing inventory levels to optimizing warehouse layouts and maintaining the right temperature, the devices can streamline inventory management and reduce the % of damaged and leftover goods.
Conclusion
The Internet of Things in the manufacturing industry is also known as IIoT (Industrial Internet of Things). The technology is still evolving into something bigger and greater. Manufacturers should be ready to make the most of advanced applications and analytics to become industry leaders in the global market.
Partnering with Trumould Injection Molding Company will help manufacturers overcome challenges and increase ROI. Talk to us for more information.
Ref:
https://www.telefonica.com/en/communication-room/blog/impact-and-applications-of-iot-in-industry-4-0-and-the-manufacturing-sector/
https://hashstudioz.com/blog/the-internet-of-things-and-its-impact-on-the-manufacturing-sector/
https://www.ibm.com/topics/internet-of-things
https://www.sam-solutions.com/blog/iot-in-smart-manufacturing/
https://www.statista.com/topics/2637/internet-of-things/