Revolutionizing Healthcare Manufacturing
Medical Injection Molding Overseas Company in USA
- Trumould is a leading Medical Injection Molding Overseas Company, serving clients in the USA and India with precision and quality.
- Medical injection molding refers to the process of manufacturing medical components, devices, and equipment using injection molding techniques. It involves injecting molten materials, often medical-grade plastics or silicone, into molds to produce intricate and precise shapes. This technology has revolutionized the healthcare industry by enabling the cost-effective mass production of vital medical tools.
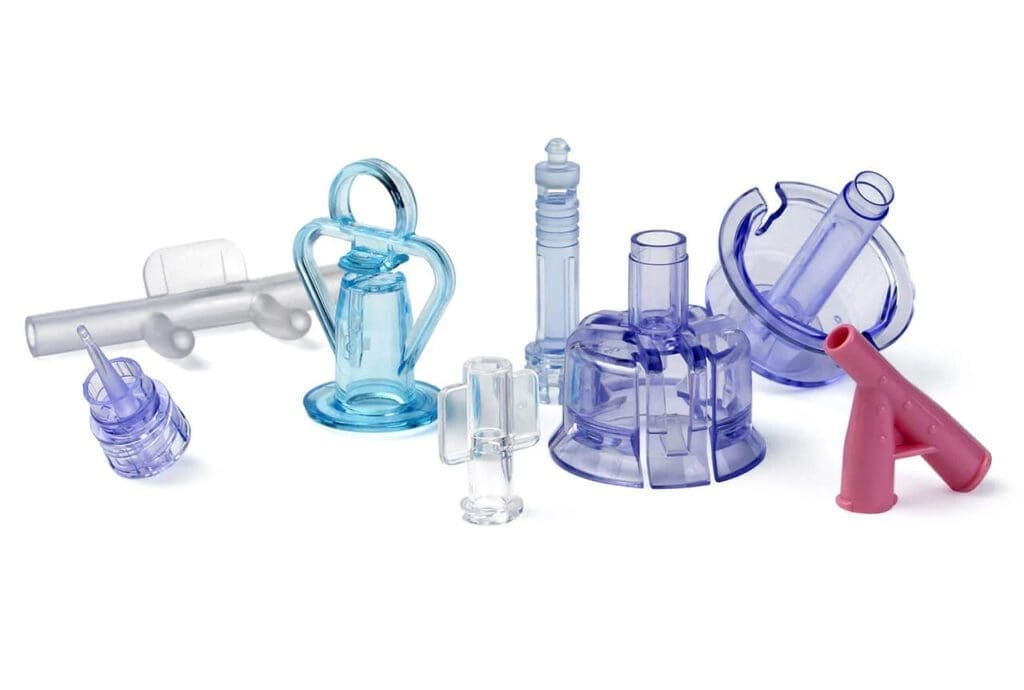