Trusted Custom Injection Molding Company
Plastic Injection Molding Company in India
Welcome to TruMould, your premier plastic injection molding company in India. At TruMould, we specialize in delivering high-quality, custom plastic injection molding services tailored to meet the diverse needs of industries such as automotive, healthcare, consumer goods, and electronics. Our state-of-the-art technology and skilled engineers allow us to produce complex shapes with excellent dimensional accuracy and consistency. Whether you are looking to launch a new product or streamline your production process, TruMould provides innovative solutions that ensure precision, durability, and cost-effectiveness. Get an instant quote today and experience the TruMould difference in your manufacturing process.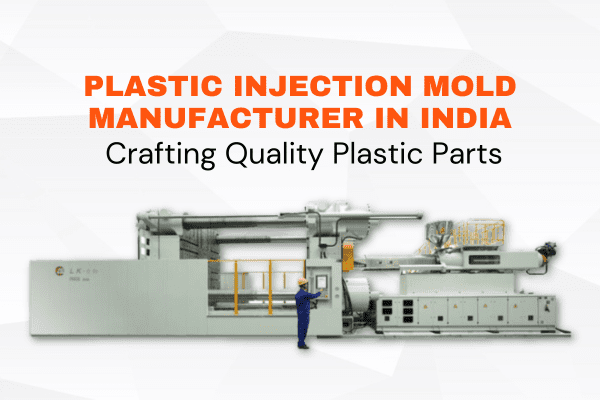