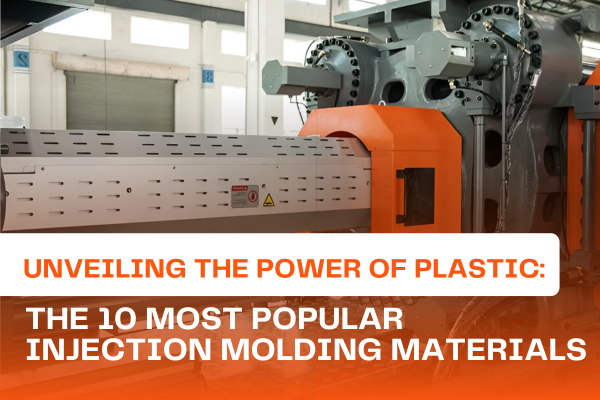
Unveiling the Power of Plastic: The 10 Most Popular Injection Molding Materials
Introduction: Plastic injection molding is a versatile manufacturing process, and the choice of materials plays a pivotal role in shaping the final product’s characteristics. In this comprehensive exploration, we delve into the 10 most popular injection molding materials, shedding light on their unique properties and applications. As the demand for precision and efficiency in manufacturing rises, plastic injection molding companies are increasingly relying on these materials to meet diverse industry needs.
- Polyethylene (PE): Widely recognized for its versatility, Polyethylene is a go-to material in plastic injection molding. Its low cost, excellent chemical resistance, and suitability for various applications make it a favorite in industries ranging from packaging to automotive components.
- Polypropylene (PP): Known for its high melting point and exceptional chemical resistance, Polypropylene is a preferred choice for products requiring durability and strength. Plastic injection molding companies often utilize PP for creating containers, automotive parts, and medical devices.
- Polystyrene (PS): With its lightweight and cost-effective properties, Polystyrene is commonly used in packaging and disposable products. Plastic injection molding transforms PS into items like food containers, trays, and disposable cutlery.
- Acrylonitrile Butadiene Styrene (ABS): ABS is renowned for its toughness and impact resistance, making it an ideal choice for products that require durability. Plastic injection molding companies often use ABS for producing automotive components, electronic housings, and consumer goods.
- Polyvinyl Chloride (PVC): PVC’s excellent chemical resistance and flame-retardant properties make it suitable for a variety of applications, including pipes, cable insulation, and medical devices. Plastic injection molding companies leverage PVC’s versatility in creating both rigid and flexible products.
- Polyethylene Terephthalate (PET): PET’s transparency, lightweight nature, and recyclability make it a popular choice for packaging materials, especially in the production of bottles for beverages and personal care products.
- Nylon (Polyamide): Nylon is prized for its strength, flexibility, and resistance to abrasion. Plastic injection molding companies often use nylon for manufacturing gears, bearings, and other components in the automotive and industrial sectors.
- Polycarbonate (PC): Known for its exceptional impact resistance and optical clarity, Polycarbonate is a preferred material for products such as eyewear lenses, electronic components, and automotive parts.
- Polyoxymethylene (POM): POM, also known as Acetal, is valued for its high stiffness, low friction, and excellent dimensional stability. Plastic injection molding companies commonly employ POM in the production of precision parts, gears, and mechanical components.
- Thermoplastic Elastomers (TPE): TPE combines the characteristics of rubber and plastic, offering flexibility and resilience. Plastic injection molding companies use TPE in applications where soft-touch features are essential, such as grips, seals, and medical devices.
Conclusion
As the plastic injection molding industry continues to evolve, the careful selection of materials remains pivotal in achieving optimal results. Plastic injection molding company, armed with a deep understanding of the properties and applications of these 10 popular materials, are well-equipped to deliver innovative solutions across a multitude of industries. The dynamic interplay between material science and injection molding techniques underscores the versatility and enduring significance of plastic in the modern manufacturing landscape.