What is On Demand Injection Moulding ?
On-demand injection molding is a form of manufacturing, a process that allows manufacturers to produce specific quantities of items as and when they are needed. This reduces the burden of maintaining a high level of inventory, and the risks associated with overproduction or underproduction.
Injection molding is a process where materials are injected into a mold to produce parts or products. The process involves melting plastic pellets and injecting them into a mold cavity where it cools and hardens to the configuration of the cavity. It’s a versatile manufacturing process used for producing parts in large volumes, from the simplest to the most complex shapes.
The ‘on-demand’ aspect means that the injection molding is done based on the actual demand of the parts, leveraging digital platforms to streamline the design, order, and manufacturing process. It facilitates small quantity orders for prototypes or customization in larger batches, thus providing a lot of flexibility and cost-effectiveness for manufacturers.
The Emergence of On-Demand Injection Molding
On-demand injection molding is rising in popularity due to the shift in consumer and market demand. Modern customers prefer personalized products, and the market is increasingly becoming volatile. On-demand manufacturing facilitates flexibility and quick adjustments to these ever-changing demands.
Furthermore, digitalization has paved the way for this shift. With digital platforms, companies can now easily upload their design files, get instant quotes, and place orders. This technology has significantly reduced the lead time compared to traditional manufacturing methods. Trumould is pioneering this shift in injection molding by developing a tech-enabled platform that specifically solves injection molding issues.
Drawbacks of Traditional Injection Molding
Traditional injection molding is an established process that’s been utilized for many years. However, in the face of modern market requirements, certain challenges associated with the procurement process for traditional injection molding have become evident.
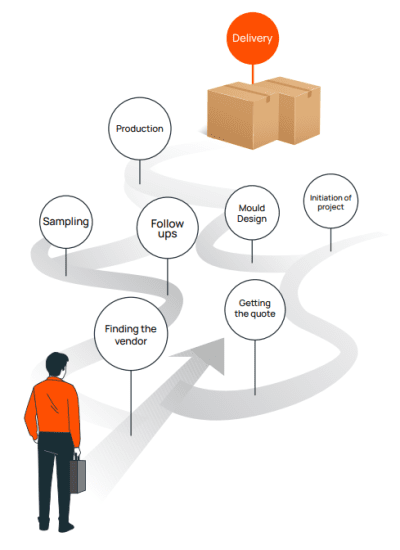
Traditional Injection Molding Process
Finding the Right Vendor
Finding a reliable and qualified vendor is a significant task in itself. Companies must thoroughly research and compare numerous factors, such as a vendor’s capabilities, expertise, production capacity, and past performance. Factors like geographical location, reputation, and ethical practices also matter. All these aspects take time to analyze, and the process may result in delays and increased overhead costs.
Getting a Quote
After identifying a potential vendor, the next step is obtaining a quote for the required services. However, this process in traditional manufacturing is rarely quick. It typically takes about 5 to 10 business days to receive a quote. Furthermore, quotes for the same part can vary widely between vendors, causing confusion and often requiring additional negotiation and clarification.
Post-Order Communication Challenges
Once the order is placed, maintaining communication with the vendor can be problematic. Vendors may not always be readily available to provide updates or address queries. This lack of transparency can lead to uncertainty and anxiety about the timeline for order completion and delivery.
Time Delays from Vendor Side
Another common issue in traditional injection molding is vendors failing to meet delivery commitments. These delays can disrupt production schedules, lead to financial setbacks, and potentially harm the client’s brand reputation.
Quality Control Issues
Quality assurance varies significantly between vendors. Each vendor has its own quality control standards, which may not align with the customer’s expectations. This inconsistency can result in higher defect rates, product returns, and customer dissatisfaction.
Logistical Complexities
Logistics is often another hurdle, especially when dealing with overseas suppliers. Customers may need to manage their own logistics to transport the parts, increasing overall product costs and potentially leading to delivery delays and added complications.
Summary
While traditional injection molding remains a foundational process in manufacturing, its procurement challenges—including delays, inconsistent quality, and logistical issues—highlight the limitations of the model. These challenges have driven the rise of on-demand manufacturing, offering a more flexible, faster, and efficient alternative better suited to modern production needs.
Advantages of On-Demand Injection Molding
On-demand injection molding is rapidly becoming a preferred choice due to the several advantages it offers over traditional manufacturing. Let’s delve deeper into some of these advantages, supplemented by specific examples related to injection molding.
-
Scalability and Flexibility
On-demand injection molding enables companies to produce small batches for prototype testing or scale up for full production runs. This approach eliminates the high costs of producing and storing unnecessary parts, significantly reducing inventory expenses.
Automotive Industry Example
In the automotive industry, engineers often need parts like door handles, panels, buttons, and knobs in limited quantities for prototype vehicles. On-demand injection molding delivers these parts quickly and efficiently, without requiring the production of thousands of units upfront.
Quick Iterations and Time Efficiency
The digital nature of on-demand manufacturing allows teams to make design alterations and iterations faster, speeding up the product’s time to market.
Medical Device Example
Manufacturers of medical devices frequently go through multiple iterations and validation steps. With on-demand manufacturing, they can swiftly implement modifications and adjustments, accelerating the product development cycle.
Cost Efficiency
On-demand injection molding minimizes upfront costs because it eliminates the need for large material inventories or storage space. It also offers real-time pricing, allowing companies to manage budgets more effectively.
Startup Use Case
A startup developing a new consumer electronics device can use on-demand injection molding to create parts like casings, buttons, or other components. They can begin with a small batch for testing, then scale up production as demand increases—all while maintaining tight control over costs.
Quality and Consistency
Advanced digital technologies power on-demand injection molding, delivering high-quality and consistent results. The process ensures repeatability and gives manufacturers greater control over production standards.
Aerospace Industry Example
In the aerospace industry, where precision is non-negotiable, on-demand injection molding ensures every component—from interior cabin fixtures to parts within the engine—meets exact specifications and maintains consistent quality.
Sustainability
On-demand injection molding supports sustainability by enabling manufacturers to produce only what they need. This reduces waste and aligns with growing environmental priorities.
Toy Manufacturing Example
A toy manufacturer using on-demand injection molding can reduce plastic waste by producing items only when there’s actual demand, avoiding overproduction and surplus inventory.
Final Thoughts
In summary, on-demand injection molding offers an efficient, flexible, and cost-effective manufacturing solution. It meets the expectations of modern consumers and adapts to dynamic market conditions. With its wide-ranging benefits, this approach is poised to transform the future of manufacturing.